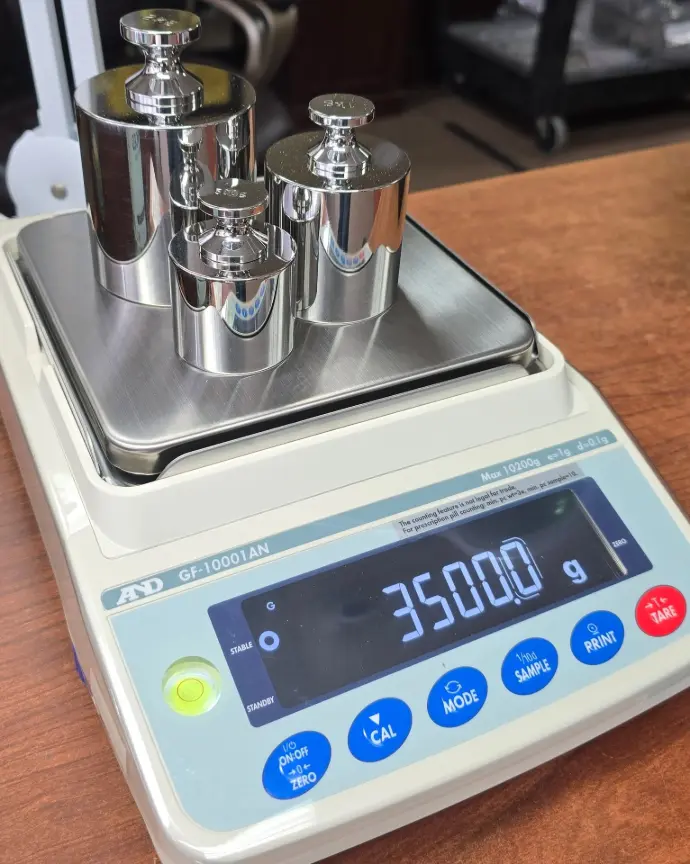
What is Scale Calibration?
Calibration of a scale is a procedure whereby a technician uses known test weights that are certified by the State of Florida Bureau of Weights and Measures to adjust the response of an electronic or mechanical weighing device during the following tests:
|
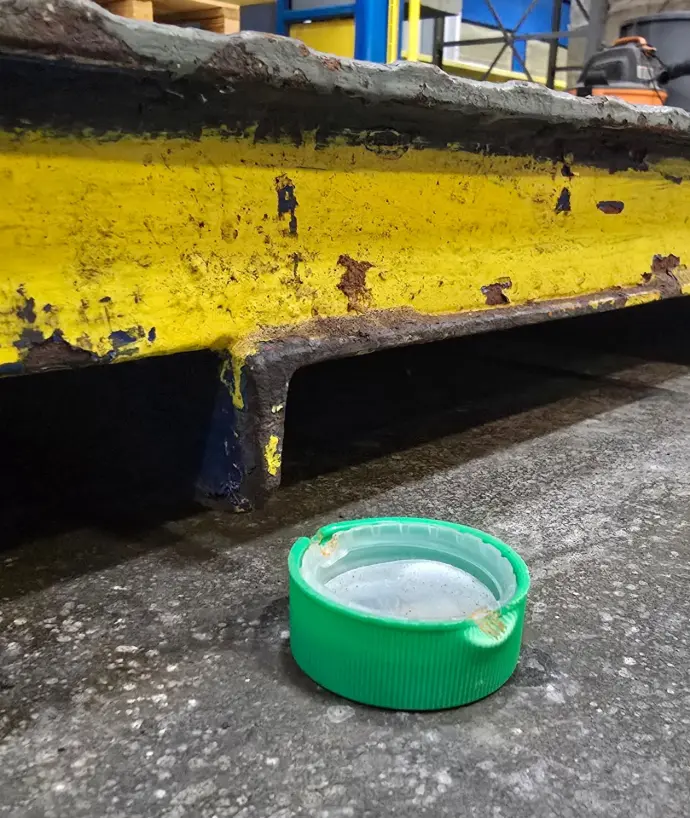
Why is Scale Calibration Needed?
- Debris and dirt will build up around scales causing alternate load paths that will affect accuracy
- All new scales must be calibrated when first placed into service at an end users location.
- With the prevalence of foreign manufactured weighing devices we always see new scales displaying a lighter weight on the device than the known test weight here in Central Florida due to the centrifugal force of the earths rotation compared to where the device was made and initially calibrated
- If you buy a device from an online retailer, please call us to get it inspected prior to placing it into service at your facility
- Any scale will, in time, drift away from its original calibration. Wearing of mechanical components, age, and degree of use will all contribute to calibration drift
- The Florida Department of Agriculture Weights and Measures requires that any scale used to sell a commodity or service must be inspected and certified as to its accuracy BEFORE it is used in a legal for trade application for the general public.
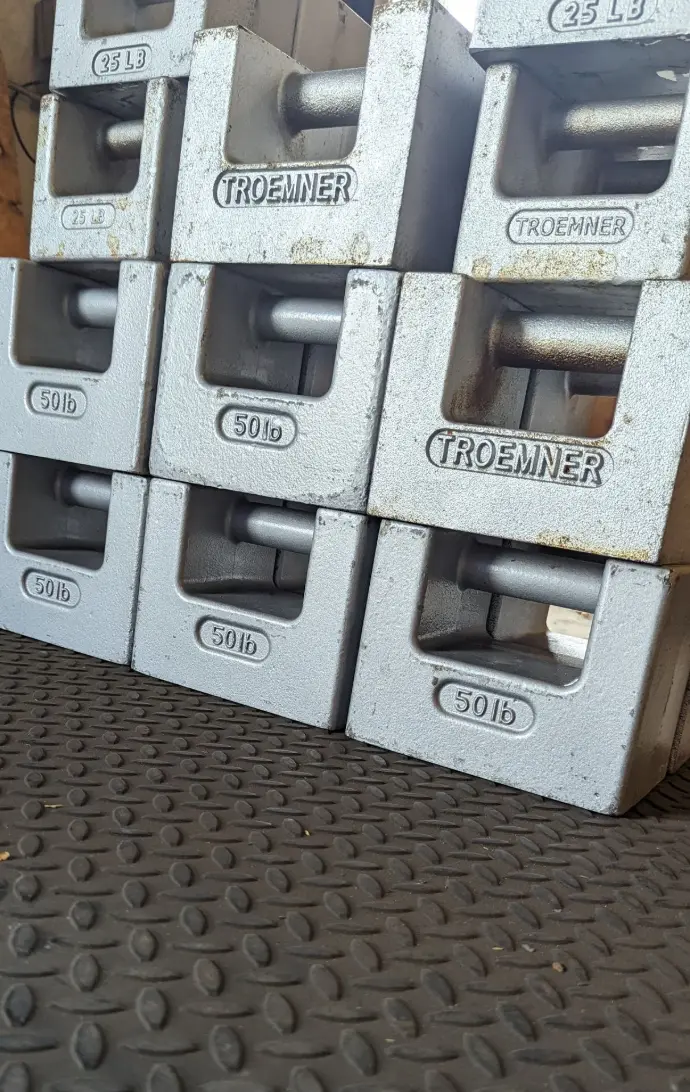
How Often Must I Calibrate?
There are many factors to consider when deciding on your frequency interval.
- Is the scale operating in a hostile environment?
- How often is the scale being used? One, two, Three shifts a day?
- How critical to your entire operation is your scale? Can your business operate without it? Do you have an extra device you can use while one is down for maintenance?
- Are there any quality control requirements like local or federal contracts requiring proof of calibration?
- SQF USDA FDA ISO Standards or any other regulatory agency or third part auditor that requires your weighing devices to have regular calibration inspections?
- How long can you afford to have a scale onsite that is out of calibration and shipping too much or too little product?
Typically we would recommend a more frequent calibration interval to start. After a history is developed for each device we can then assist you reducing the frequency of inspections while minimizing the risk of using a device out of tolerance at your facility.
Added Benefits to Regular Calibration Customers!
Priority Scheduling
While we do everything we can to keep all of our customers downtimes at a minimum, we will rank regular calibration customers & customers that purchase new equipment from us at a higher priority on the schedule when emergency tickets are entered in the system
Reduced Service Rates
We offer a slightly discounted travel rate and hourly service rates for customers that have at least a Biannual calibration agreement active for their account
Familiarity with your devices
Since our service technicians are at your facility at least twice a year we know your equipment and can better plan and execute emergency repair requests if they come up between regularly scheduled visits